Die casting is an essential part of Malaysia’s manufacturing industry, contributing significantly to the production of high-precision metal components for various sectors. This process involves forcing molten metal into a steel mold or die under high pressure, creating intricately shaped parts with exceptional surface finishes and precise dimensions. In Malaysia, the die casting industry has seen steady growth over the years, driven by increasing demand from key industries such as automotive, electronics, and home appliances. As manufacturers seek more efficient and cost-effective production methods, die casting continues to offer a reliable solution, particularly for mass production where consistency and speed are paramount.
One of the most significant contributors to the demand for die casting in Malaysia is the automotive sector. With Malaysia being one of Southeast Asia’s key automotive manufacturing hubs, the need for lightweight and durable metal components is crucial. Die casting offers the ability to produce parts such as engine components, gearboxes, and structural parts that are strong yet light, a necessity in modern vehicle design, especially with the increasing focus on fuel efficiency and sustainability. Moreover, with the rise of electric vehicles (EVs), the automotive industry requires even more aluminum die-cast parts to reduce vehicle weight and enhance energy efficiency. Malaysian die casting companies are well-positioned to meet this growing demand, offering high-quality parts that meet stringent automotive standards.
The electronics industry is another significant driver of Malaysia’s die casting sector. As Malaysia is a major player in global electronics manufacturing, die casting is essential for producing the intricate metal parts used in devices such as smartphones, laptops, and home appliances. The precision offered by die casting allows manufacturers to create components with tight tolerances, ensuring the reliability and performance of the final products. As electronic devices become smaller and more advanced, the demand for die-cast parts that can meet the challenges of miniaturization has grown. Malaysian die casting companies have adapted by adopting cutting-edge technologies and techniques to produce smaller, more complex parts efficiently.
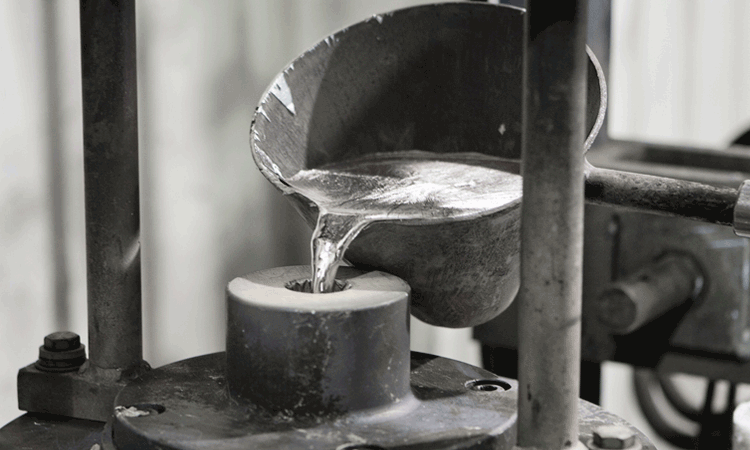
Sustainability is becoming a central focus for the powder coating malaysia, aligning with global trends toward greener manufacturing practices. The industry is gradually shifting towards using more environmentally friendly processes, such as employing recycled materials and improving energy efficiency during production. Many Malaysian die casting companies are now integrating sustainable practices, not only to reduce their environmental footprint but also to meet the growing demand from international clients who prioritize eco-friendly production. In addition to material recycling, advancements in die design, such as optimizing mold cooling systems and reducing waste, are helping manufacturers enhance both productivity and sustainability. This commitment to sustainability is positioning Malaysia’s die casting industry as a forward-thinking player in the global manufacturing market.
The development of infrastructure and the availability of skilled labor have also contributed to the growth of Malaysia’s die casting industry. The Malaysian government has played an active role in supporting industrial development, offering incentives, tax breaks, and facilitating foreign investments in the manufacturing sector. This has encouraged local companies to invest in advanced die casting equipment and technology, improving the quality and efficiency of their operations. Furthermore, Malaysia’s focus on technical education and vocational training has ensured a steady supply of skilled workers who are familiar with modern manufacturing techniques. This skilled workforce is crucial in maintaining the high standards required in die casting, especially as the industry moves towards more complex and precision-driven production methods.
Innovation remains at the core of the die casting industry in Malaysia, with companies continuously exploring new technologies to improve production efficiency and product quality. The adoption of automation and digitalization in die casting processes has allowed manufacturers to produce more consistent and high-quality components while reducing human error and production times. Advanced computer-aided design (CAD) and simulation tools are also being utilized to optimize mold designs, ensuring the highest level of precision and reducing trial and error in the manufacturing process. These technological advancements have enabled Malaysian die casting companies to remain competitive in a fast-evolving global market, where quality, speed, and efficiency are key drivers of success.
In conclusion, die casting in Malaysia is a crucial part of the country’s industrial framework, providing essential components to a range of industries including automotive, electronics, and consumer goods. The industry’s ability to produce high-quality, precision-engineered metal parts with cost efficiency makes it an attractive option for mass production. With a strong emphasis on sustainability, innovation, and the development of a skilled workforce, the Malaysian die casting sector is well-positioned to meet the growing global demand for die-cast components. As industries continue to evolve and prioritize efficiency and environmental responsibility, die casting in Malaysia is set to play an even more prominent role in the future of manufacturing.